OVERVIEW
The correct selection of a sealant must consider the purpose of the joint, the size of the joint deformation, the size of the joint, the joint substrate, the environment in which the joint contacts, and the mechanical properties that the sealant is required to achieve. Among them, the size of the joint is determined by the type of joint and the expected size of the joint deformation.
To ensure the optimal service life and performance of the sealant, the correct selection of sealant must be carefully considered. Generally, three steps can be taken to ensure that the sealant reaches its optimal design life.
- 1. Design seams scientifically and reasonably according to usage needs and environment;
- 2. Determine the performance indicators that the sealant needs to meet in the designed interface;
- 3. Based on the determined performance indicators, it is recommended to select the adhesive and conduct necessary compatibility and adhesion tests to ensure that the selected product meets the requirements.
Sealants for construction perform the following three functions through the bonding process:
- 1. Capable of filling the gap between two or more substrates to form a seal:
- 2. Forming a barrier through its own physical properties and adhesion to the substrate
- 3. Maintain sealing tightness under its expected lifespan, working conditions, and environment.
The main factors that determine the function of the sealant include its movement capability, mechanical properties, adhesion, durability, and appearance. Mechanical and mechanical properties mainly refer to indicators such as hardness, elastic modulus, tensile strength, tear resistance, solidification, and elastic recovery rate. When applying sealant, the main usage requirements that should be considered are the tack free time, debonding time, sagging, shelf life (for two-component adhesives), extrudability, deep curing speed, non foaming, cost, color, and linear shrinkage during curing; At the same time, it is necessary to consider the aging properties of the sealant, including its UV radiation resistance, high and low temperature mechanical properties, thermal hydrolysis, thermal aging, and oxidation resistance.
Adhesion is a process that includes the preparation, application, curing, and maintenance of sealant. The quality of adhesive performance is directly related to the bonding material, sealant, and adhesion process. Therefore, when carrying out construction, the influence of three factors should be comprehensively considered. Only by adjusting the three factors reasonably and combining them organically can the ideal adhesion be achieved, and any problem in any link may lead to the failure of the adhesion.
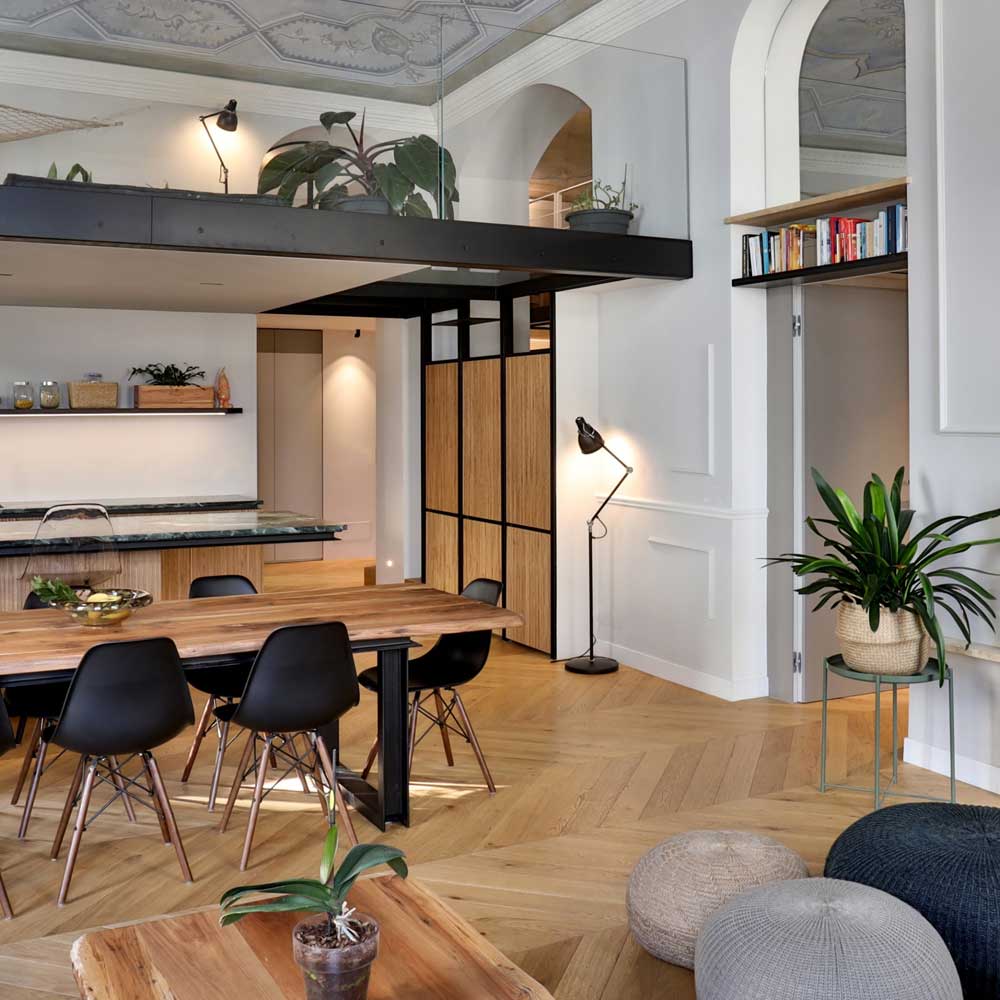
Silicone sealant used in construction mainly provides weather resistant sealing and structural sealing. In addition to good interface design, corresponding construction process specifications must also be followed during the construction process.
There are five basic requirements for proper interface surface treatment and gluing:
- The interface surface must be clean, dry, free of dust and frost;
- If primer is required, it must be applied to a clean surface;
- Use back-to-back materials or adhesive tape as required;
- When applying the sealant, it is necessary to fill the interface gap with sealant;
- Scraping is to ensure smooth seams, correct shape, and complete contact with the substrate.
Silicone sealant can also be considered as an adhesive due to its chemical structure. Silicone sealing adhesion is a natural chemical reaction, so the correct usage steps are very important. Due to the application of OLIVIA silicone sealant in many different environments and states, construction process specifications cannot be regarded as a complete and comprehensive quality assurance program. Quality management of construction must also be carried out, and on-site adhesive testing must be carried out to ensure good adhesive strength and verify any suggestions regarding the adhesive.
In the quality management of sealant construction, the adhesion and compatibility of sealant and base material must be considered, including supporting rod, double-sided tape strip and other auxiliary materials. To leverage the superior performance of silicone sealant, it is necessary to choose different silicone sealants based on different construction environments, requirements, and materials, and master standardized construction techniques. Unstandardized construction techniques often limit the superior performance of sealants, such as cleaning the surface of the substrate, the amount of primer used, improper aspect ratio, uneven mixing of two component sealants, and the use of incorrect cleaning solvents or methods, which can affect the adhesion of sealants and even lead to adhesion failure, such as improper attachment selection leading to bubbles and discoloration of the sealant. So the selection of sealant and the correctness of the construction process are crucial. By introducing these functions, it can help to select the appropriate sealant correctly.
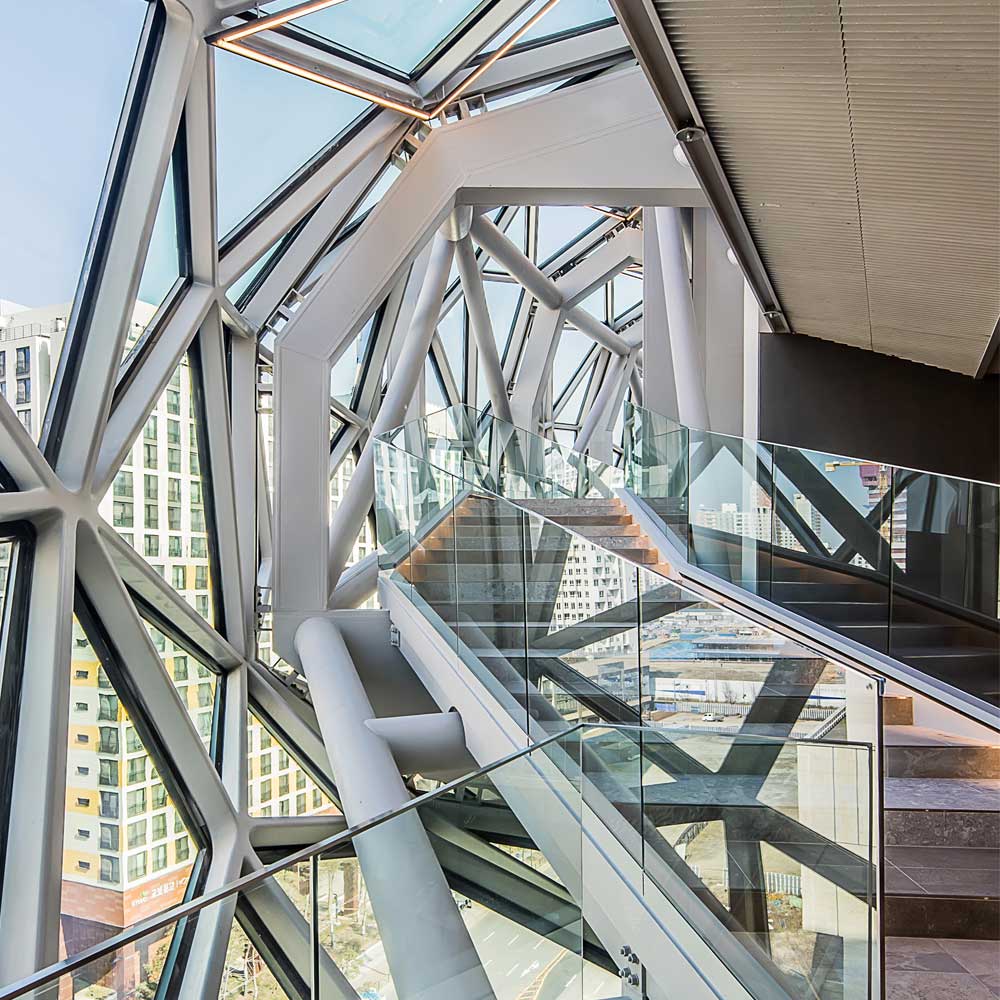
Waterproof and Weatherproof Seal
Some non silicone sealants are prone to aging over time and under the influence of harmful factors in the environment, especially under ultraviolet radiation. Therefore, when choosing a sealant, the service life of the sealant should be considered. Waterproof sealing is used to fill gaps between materials to prevent wind, rain, dust, etc. from passing through the gaps. Therefore, the sealant must fully adhere to the substrate, so that it can overcome changes in joint size caused by substrate movement during extension or compression. OLIVIA silicone sealant has good UV resistance, can maintain almost constant modulus, and its elasticity does not change within the temperature range of -40 ℃ to+150 ℃.
Low performance sealants are mainly used to fill gaps under basic static conditions to prevent the entry of dust, rain, and wind. However, excessive shrinkage, hardening over time, and poor adhesion can affect their effectiveness. Compatibility, adhesion, and chemical effects must be considered when using them.
Structural Seal
The sealant used for structural sealing mainly adheres to two types of substrates. At the same time, it can overcome the stress encountered: tension and compression stress, shear stress. Therefore, before sealing, the structural strength of these joints should be confirmed, so that they can be expressed in quantity when calculating engineering needs. Structural strength is expressed in terms of modulus and tensile strength. Structural sealants need to reach a certain level of strength. Another important condition for structural sealing is that the bonding between the seal and the substrate does not damage over time. OLIVIA silicone structural sealants have reliable performance, long service life, and are suitable for structural sealing.
Precautions For Selecting Silicone Sealant For Construction
The correct selection of sealant not only involves selecting materials with appropriate physical and chemical properties, but also considers the type and properties of the sealing substrate, joint design (including support or embedded materials), expected performance, production requirements, and economically cost-effective costs, all of which are considered. The following list is commonly used in the construction industry to select sealants.
Attached Sheet No.1
Movement of connecting points required |
Fungicide |
Minimum connection width |
Anti-radiation |
The strength required |
Insulation or conduction requirements |
Chemical Environment |
Colors |
Working Temperature |
Resistance to soaking or abrasion |
Construction Temperature |
Curing Speed |
Sunlight and weathering intensity at work |
Low grade or continuous water soaking |
Lifetime |
Accessibility of joints |
Normal climate at time of application |
Primer |
Material costs: initial and lifetime |
Special cleaning requirement |
Installation costs |
Dryness |
Other requirements |
Other limiations |
Post time: Aug-02-2023